What is SLES?
SLES is an acronym for a compound of Sodium Lauryl Ether Sulfate. This compound is referred to as a surfactant (Surface-active agent) and lowers the surface tension between a liquid and a gas, a liquid and a solid, or between two liquids.
Where is SLES used?
SLES is used across multiple sectors in both the sanitary and industrial markets. Primary uses are for SLES to be used as foaming agents, degreasing agents, and cleansers, however, there are many more uses for SLES within the printing and dyeing industry, petroleum industry, and leather industry. Some common household products that use SLES are shampoos, soaps, toothpaste, and liquid detergents.
What concentration of SLES is used during manufacturing?
SLES is often delivered at ~70% concentration and then diluted down on-site to ~27% for usage. Due to the cost of procuring readily diluted ~27% SLES, it is more cost-effective for companies to dilute themselves.
There is also the element of fine-tuning the final result, should the end product require a small change in final concentration. Another issue for 70% SLES is the difficulty in processing it, due to the high viscosity and the rapid viscosity decrease once below a certain percentage threshold.

How to dilute SLES
Reducing the percentage of 70% SLES is, in principle, easy. By mixing water + additives with 70% SLES, you can create a diluted SLES concentration.

However, to move ~70% is very different to <27% SLES due to the viscosity difference, and as such, requires fundamentally different pumping technologies.
In the Tapflo SLES Mixing and Dilution Unit, we utilise a Progressive Cavity Pump for 70%, and a Centrifugal Pump for <27%.
The water used to dilute 70% can be almost any grade, providing it is acceptable in the final product recipe. This can be Raw Water, Reverse Osmosis Water, Demin Water etc.
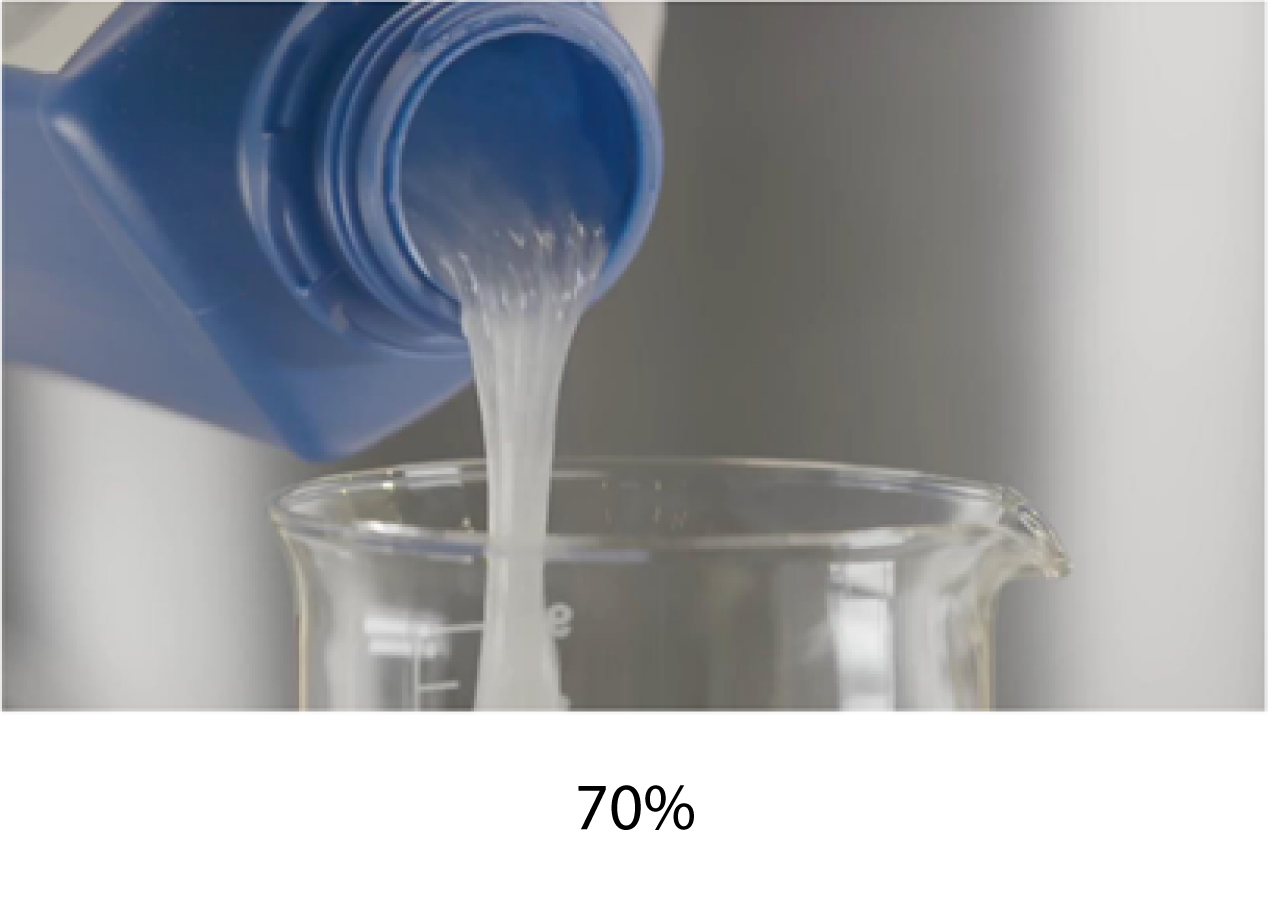
Pre-diluted SLES
There are three main issues when opting for pre-diluted 27% SLES:
- High cost
- Requires a lot of space for storage
- Limited control over the diluted concentration
Based on these factors, almost all medium to large manufacturers who utilise SLES in their products will bring in 70% SLES and then dilute it down on site. This provides both cost and space-saving, as you can store less 70% and when required, dilute to 27%, which will yield more end product.
The cost is rapidly decreased as 70% SLES is sold at a lower cost than 27%, providing quick buy-back times for the mixing and dilution system. The site can also control the exact concentration of the end SLES, ensuring product recipes are correct.
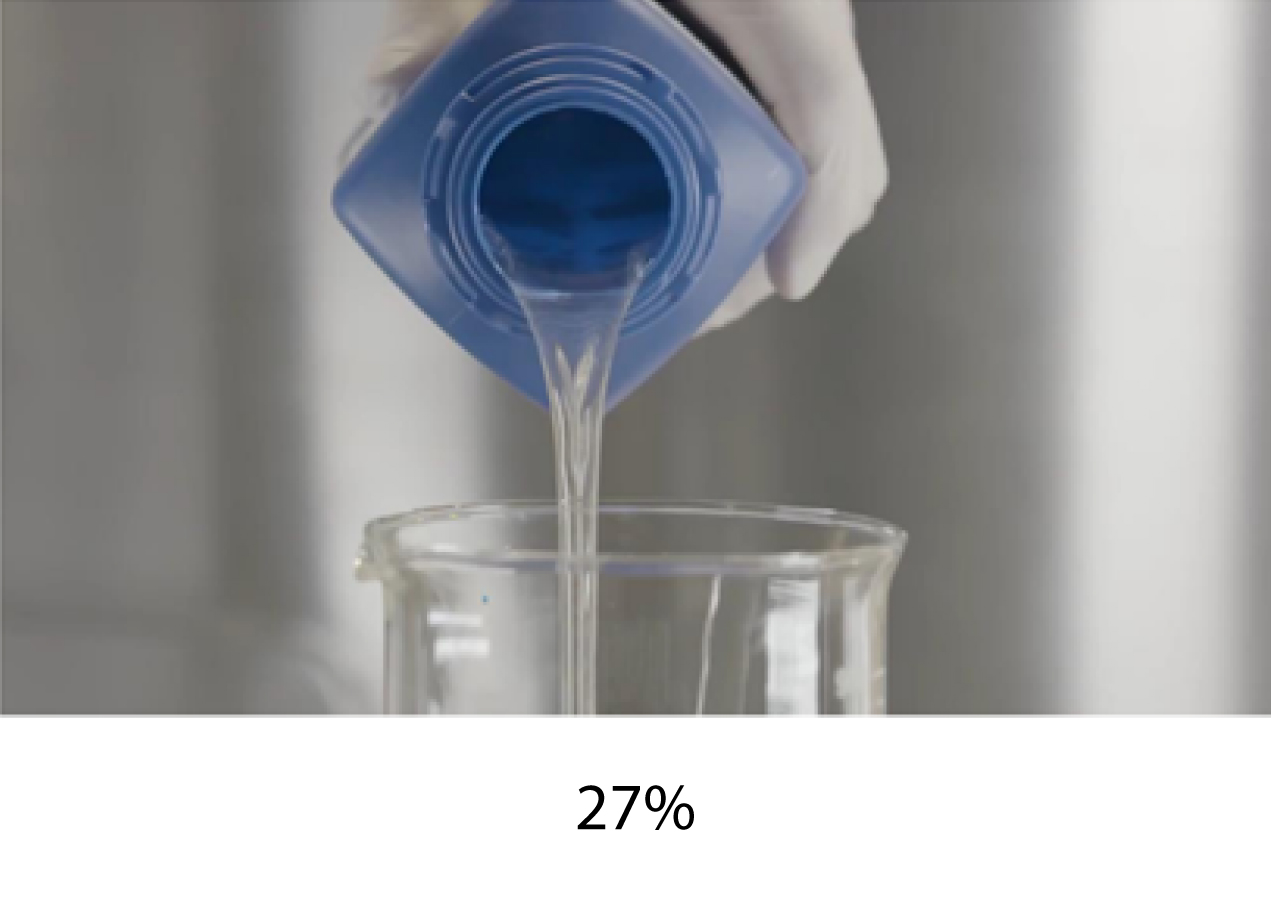
Dilution of SLES in Tank
Whilst it is possible to dilute SLES in a tank, this does present some issues and is generally not considered an efficient approach.
Diluting in a tank:
- Requires constant circulation and heating (meaning loss of energy)
- is time-consuming (takes a few hours to prepare one batch)
- is a hard process to control and regulate (inconsistencies in final concentration)
- does not provide a stable and homogeneous end product (leads to inconsistent batches and could ruin end product recipes)
In-line SLES Mixing and Dilution System
Tapflo UK offers a customised solution for in-line mixing and dilution. The final system is ideal for all sized manufacturers who use SLES and can provide buy-back times in as little as a few months.
This packaged solution comes with the necessary pumps for processing both the initial and final SLES product, including the water grade and any additives used.
The system is supplied with a 7” coloured touchscreen control cabinet, which automates and regulates the mixing and dilution, with a high level of accuracy in batching the correct amount of water to ensure the end product comes out at the correct concentration.
The system also comes complete with flowmeters, pressure and temperature sensors, actuated and manual valves, piping and support frame, inverters, and a diaphragm valve for homogenization of the SLES.
The standard package system can fit onto standard Euro Pallet dimensions (1.2 x 0.8m), providing a compact solution that can fit in almost any factory or manufacturing facility.
The system can also be tailored to more application-specific requirements, such as pre-set recipe controls of end SLES, large batching, or specific dimensions.
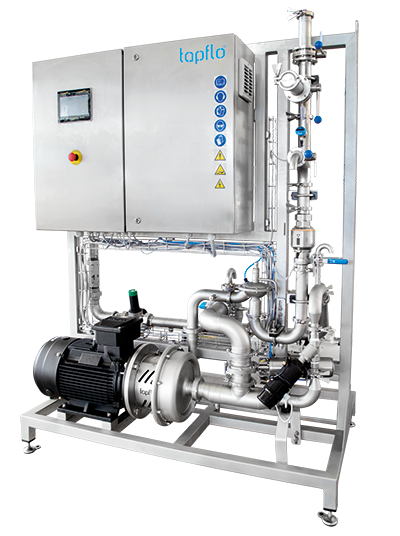