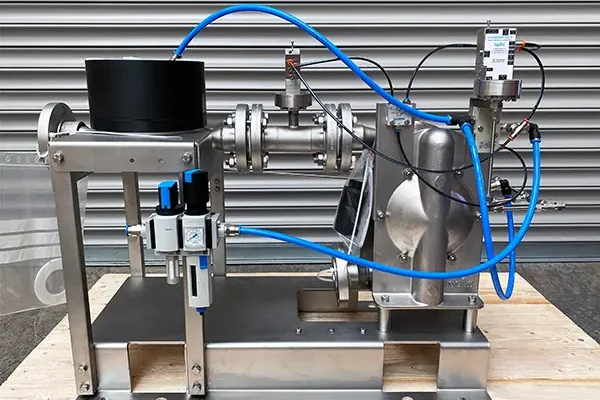
Recently, a client in the Pharmaceutical Industry approached us with an issue they were experiencing whilst pumping Methylene Chloride. The Tapflo UK technical team got on the case and came up with a purpose-built system suited to the client’s requirements.
The Application
Fluid:Â Methylene Chloride (Hazardous)
Duty:Â 4.6 m3/h @ 2Bar(g)
Temperature: 25°C
Environment:Â ATEX Zone 1 Requirements
The Methylene Chloride is transferred to a bottling area of the facility. Once the total amount of fluid is transferred, the system shuts an actuated valve, preventing further flow, and the excess fluid is recirculated back to the primary tank.
The Problem
In the past, the end user has used both Centrifugal Pumps & Air Operated Diaphragm Pumps, which on their own present problems.
The Centrifugal Pumps resulted in boiling of the fluid, due to the low vapour pressure. This is a huge risk when considering the ATEX environment.
The Diaphragm Pumps would be operating against a closed valve, resulting in dead-heading the pump. This would rupture diaphragms, allowing fluid to leak from the casing, presenting another potentially hazardous occurrence.
Our client approached us looking for a suitable turn-key solution that would eliminate these problems, solve the hazard risks, improve the quality of life for operators on site, and help reduce the cost of ownership for the solution as a whole.
The Solution
After 1 site survey with trained personnel from Tapflo UK, a suitable solution was presented that would not only tick all the boxes the end user had, but also exceed their expectations.
Barrier Diaphragm Pump:
The pump selection was made from a 1” Diaphragm Pump size which delivers the required flow and pressure without the risk of stalling, which is a common problem from oversizing AODD pumps. This was welded with 1.5” ANSI flanges to best suit the client’s existing pipework.
The pump was also manufactured as a Barrier design, which prevents hazardous leaking concerns thanks to the secondary diaphragm inside the pump, which contains the fluid inside the pump if the first diaphragm should rupture.
The diaphragms themselves are manufactured from a PTFE TFM 1705B solvent-grade material. This material choice far exceeds standard PTFE as it offers lower deformation under load, better stress recovery, better film quality, lower permeation, and reduced effect of temperature on elastic modulus.
Pulsation Dampener
The Pulsation Dampener features all the same benefits as the pump (barrier execution, ANSI flanges & PTFE TFM 1705B Diaphragms), however, this is crucial for the installation due to the pulse-y flow of the AODD pump and the dead-head scenario which occurs after filling the bottling area. The dampener significantly reduces pulsation and water-hammer effects by compressing a diaphragm inside the housing. When the pressure in the piping system decreases, the dampener supplies extra pressure to the discharge between pump strokes, therefore supplying a steady flow of the pumped medium. This pumping action created by the dampener decreases the pressure variation and pulsations.
Pneumatic Diaphragm Failure Monitoring System
The PDFM-120 utilises one of our Guardian Systems that monitors the pressure between the primary and secondary diaphragm. In the event of a rupture event, the pressure changes. The Guardian detects this, shutting off the air to the pump, in turn switching off the pump itself. The Guardian is fitted to both the pump and dampener, reducing the cost of independent guardian systems, and ensuring that under any rupture event, the system is turned off, preventing further damage.
Pneumatic Dead Head & Restart System
The PDHR-120 also utilises a Guardian System at its heart. This is fitted to the system and detects the pressure inside the pipework – if the system deadheads (due to closing of the valve to the bottling area), the system is turned off automatically, preventing damage to the diaphragms. This pneumatic system is also very unique, in that as soon as the pressure drops (due to the valve being opened, allowing the fluid to now pass through), the Guardian restarts the pump, resulting in an automated pumping process.
- 1x TXB120 SBT-3A1.5″SY4TL – Barrier Diaphragm Pump with 1.5″ ANSI 150 Flanges
- 1x DTXB120 SB-3A1.5″SY4TL – Barrier Dampener with 1.5″ ANSI 150 Flanges
- 1x PDFM-120 – Diaphragm Monitoring Kit, Monitoring Pump + Dampener
- 1x PDHR-120 – Dead Head & Restart System
- 1x 6-100-003FX – Air Treatment & Control Kit
- 1x S3184_1 – : AISI 304, Sandblasted Skid Frame
- Approximate Dimensions = 700x500x600 mm (LxWxH)
The equipment above was mounted onto a fabricated AISI 304 sandblasted skid, with supports for the dampener and forklift accessible points. It also featured an air treatment & control kit, allowing fine-tuning of the pump performance and ensuring a clean, stable supply of air was provided to the equipment.
Our Senior Sales Engineer, Kieran Turner, explains the system further in the video below: