Our client, a leading ceramics manufacturer, was facing significant challenges in handling highly abrasive ceramic slurries, resulting in frequent pump failures and costly downtime. With over 25 years of experience in delivering solutions to the ceramics industry, Tapflo UK was contacted to provide a tailored solution. Through extensive collaboration and testing, we developed a custom Diaphragm Pump configuration specifically designed to withstand the abrasive nature of ceramic slip.
Application Details
Due to the abrasive nature of their ceramic slurry, our client faced ongoing issues with their pumps rapidly wearing out. Their previous pump options, ranging from Peristaltic Pumps to plastic Air-Operated Diaphragm Pumps, were not able to offer satisfactory durability. Despite spending considerable time and resources on testing different configurations, they still experienced significant downtime and frequent repairs every 30-70 days! Critical components, including valve balls, valve seats, side housings, and diaphragms, were regularly failing, leading to operational inefficiencies and escalating maintenance costs.
Components of the System
To address these challenges, we designed a custom Low Energy Diaphragm Pump (LEAP) configuration with the following components:
- Pump Size: 2″ was chosen to meet the high flow rate demands required for large-scale ceramic production
- Inlet/Outlets: Machined solid block HDPE500, which provides superior mechanical strength and abrasion resistance
- Housing: Solid block HDPE500, 10mm thicker than standard, a modification that effectively addresses cracking due to the abrasive nature of the slip and environmental stresses (optional for less frequent operations)
- Valve Seats: Polyurethane, selected for its optimal balance of cost-effectiveness and superior abrasion resistance
- Valve Ball Stops: Polyurethane, ensuring durability in the area with the highest wear
- Sleeves (Upper and Lower): PE1000, chosen for its excellent abrasion resistance
- Diaphragms: One-piece bonded NBR, ensuring durability in harsh environments
- Valve Balls: NBR, offering the best abrasion resistance while remaining cost-efficient
These configurations were selected and refined through extensive testing, including on-site trials, to ensure longevity and efficiency.
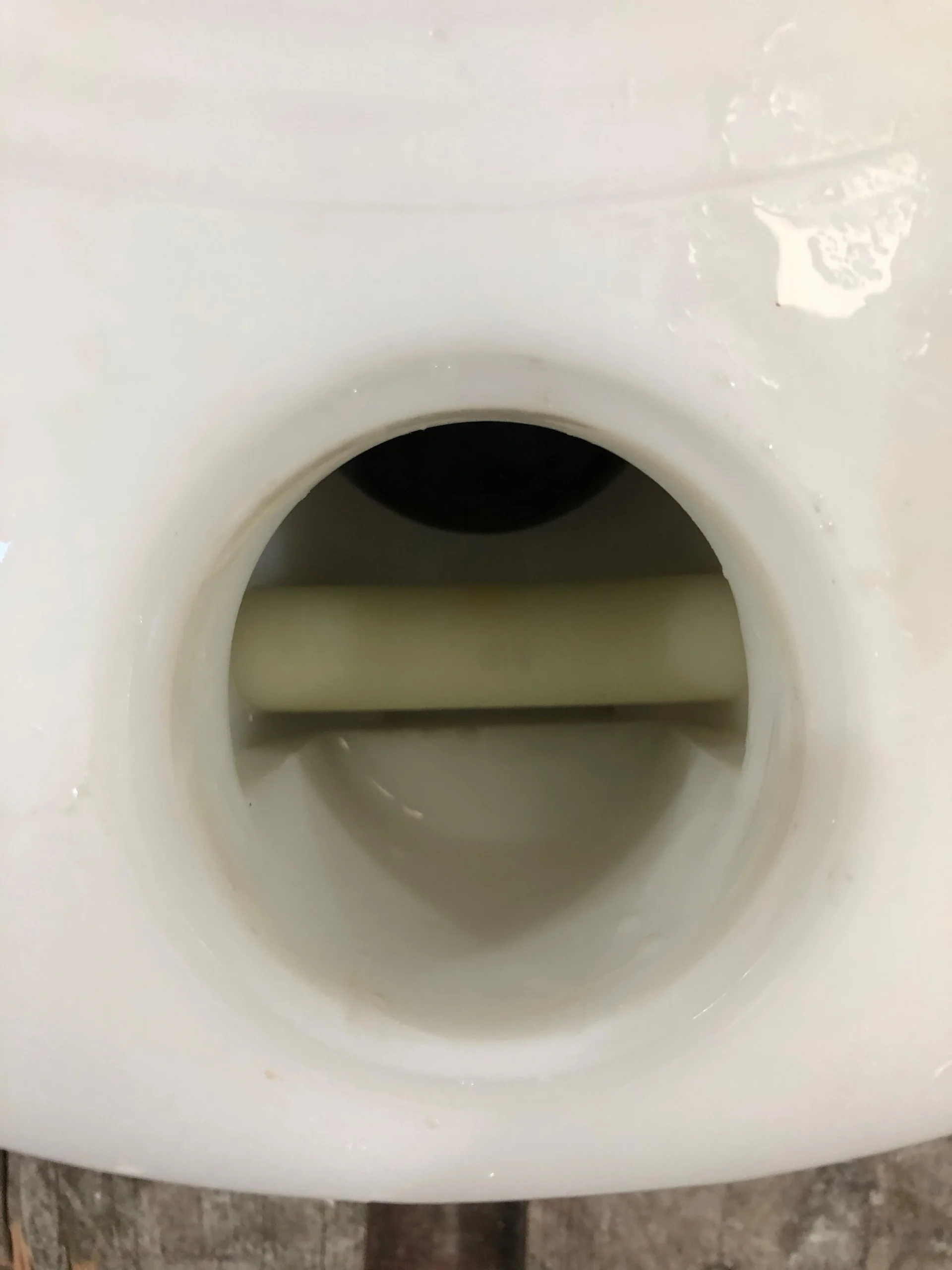
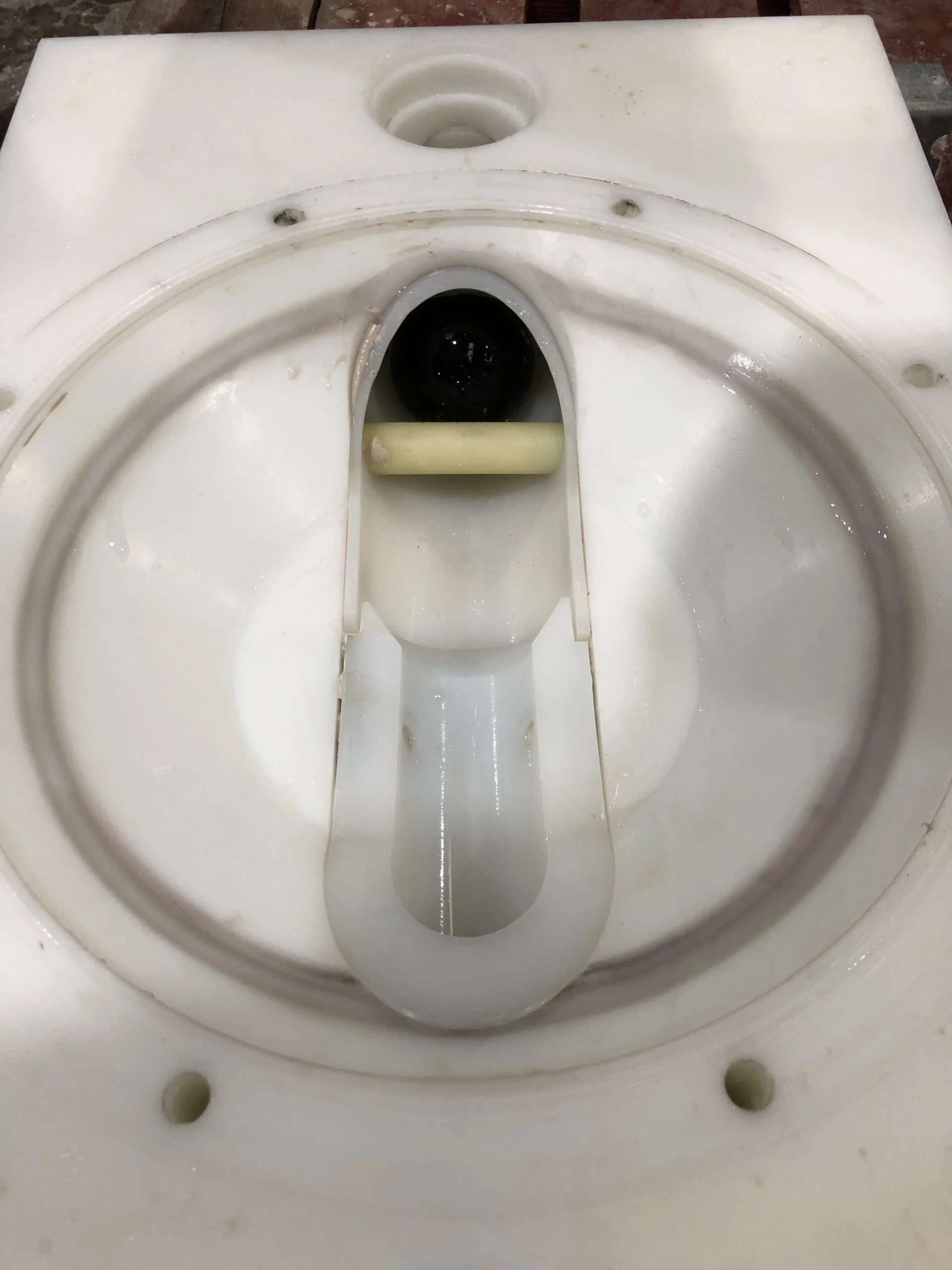
Why Low Energy Air Pump (LEAP) Technology?
In addition to the durability and performance of the Diaphragm Pump, our Low Energy Air Pump (LEAP) technology offers substantial energy savings. In independent tests against a leading American Diaphragm Pump, our LEAP unit demonstrated:
- Air Consumption: 0.103 Nm3/min at 2 Bar, compared to 0.167 Nm3/min for the competitor’s pump
- Higher Flow Rates: Despite consuming less air, the LEAP pump produced a higher flow rate, optimising operational efficiency
These results led the customer to commit to replacing 40 of their Diaphragm Pumps with Tapflo UK LEAP technology over the next 2-3 years, anticipating a 60% reduction in energy costs!
Benefits of the Solution
- Improved Durability and Reliability: The new configuration significantly reduced wear on critical components, allowing for an extended repair interval of up to 120 days—four times the previous repair frequency. Since installation, only 3 valve seats have needed replacing, even after over 30 units were deployed globally.
- Lower Maintenance Costs: The new solution drastically reduced the frequency of repairs and downtime, resulting in considerable cost savings. The pumps are now considered the industry standard for ceramic slip applications, offering substantial reductions in both parts and labour costs.
- Enhanced Flow and Efficiency: Our pumps maintain higher flow rates, ensuring production demands are met without compromising efficiency. This has enabled customers to achieve consistent and reliable performance over extended periods.
- Optimized Material Selection: The careful selection of materials, including HDPE500, PE1000, and polyurethane, guarantees exceptional abrasion resistance, contributing to the longevity of the pumps even under the most challenging conditions.
- Global Acceptance and Scalability: The pump configuration has become the norm for ceramic slurry applications in factories worldwide, with limited issues regarding wear and reliability. The scalability of the solution allows for widespread adoption across multiple production lines.
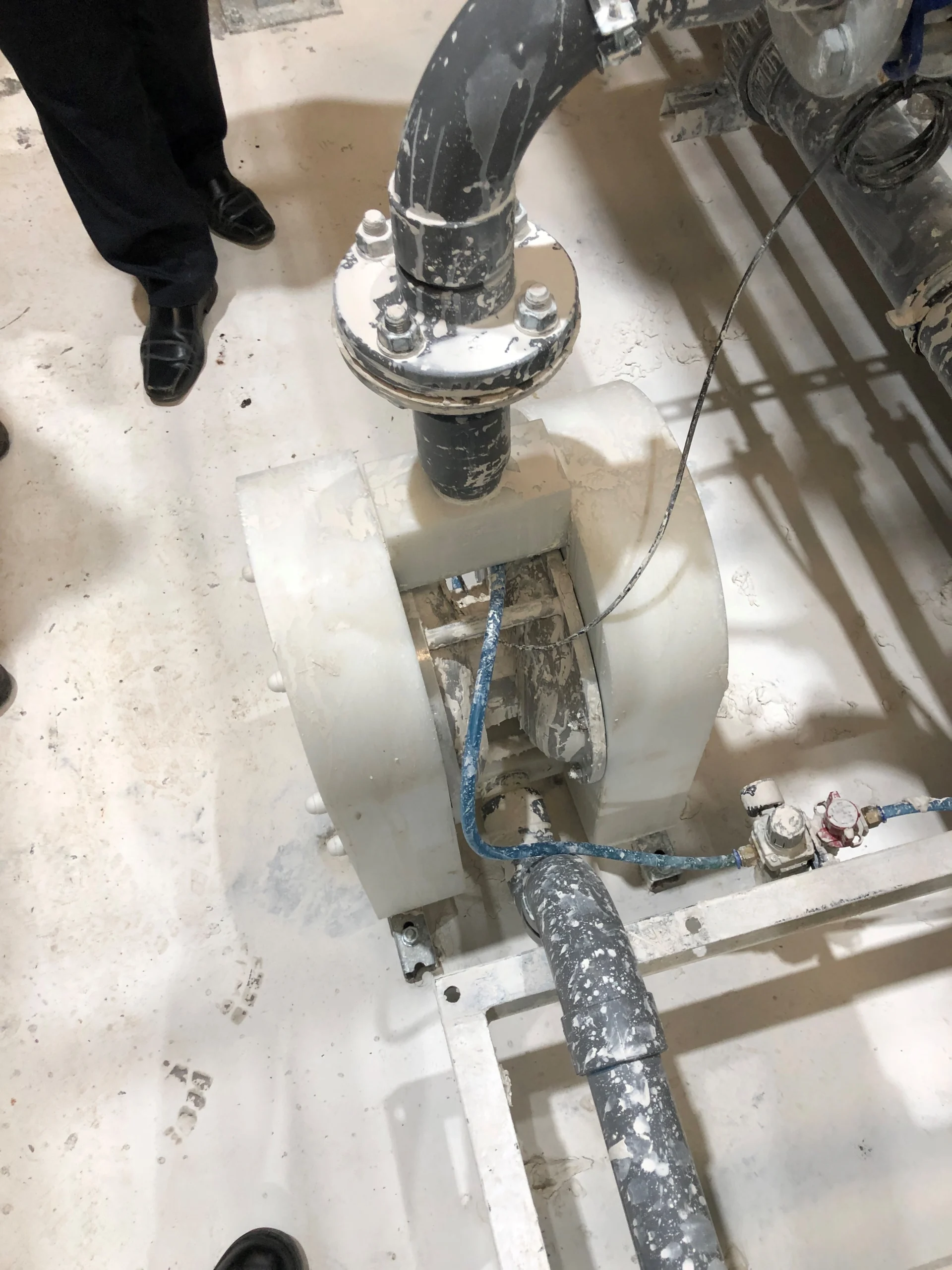
Impact & Results
Since the introduction of this pump solution in 2018, the customer has reported remarkable results:
- Over 30 units installed, with only 3 valve seats replaced
- No other components have required replacement after continuous operation for over 8 months
- The customer has now standardised this pump configuration across their global operations
The customised LEAP Diaphragm solution has transformed the customer’s ceramic slurry pumping operations, not only extending the life of the pumps but also delivering significant cost savings and enhanced efficiency.
With our extensive expertise and commitment to providing tailored solutions, we continue to set the standards for reliable and cost-effective pumping solutions in the ceramic industry.