Submersible Pumps are a foundation of modern fluid management systems, excelling in efficiency, versatility, and reliability across a diverse range of industries. From Wastewater Treatment to Construction Site Dewatering, their compact and sealed design makes them indispensable for challenging applications. This guide explores their key features, applications, and the distinctions that set them apart from standard Water and Sump Pumps.
What is a Submersible Pump?
A Submersible Pump is a purpose-built process pump designed to operate while fully submerged in the fluid it pumps. Unlike surface pumps, these compact, sealed units sit directly within the liquid, driving it upwards with high efficiency. Their submerged position eliminates many operational challenges, such as cavitation, making them invaluable across multiple industries.
How does a Submersible Pump Work?
At the heart of a Submersible Pump is a motor-driven impeller. As the impeller spins, it draws fluid into the pump, moving it through its casing and pushing it towards the surface. The surrounding liquid cools the motor, ensuring consistent performance.
- Sealed Motor Design: The motor and impeller are encased together, often within a corrosion-resistant housing. Accessories like cooling jackets and motor-filled casings enable high-temperature fluid handling
- Unique Mechanisms for Specialised Applications: Pumps tailored for unique conditions, such as slurry handling or abrasive fluids, are equipped with wear-resistant impellers and advanced sealing systems
Key Advantages of Submersible Pumps
- Energy Efficiency: Submersible Pumps eliminate suction issues by pushing water instead of pulling it, reducing energy consumption
- Ease of Use: Their design eliminates the need for frequent priming, streamlining operation
- Versatility: Suitable for fluids with varying viscosities and solids content, including clean water, sewage, slurry, and even chemicals (depending on the design), across various environments such as wells, sumps, tanks, and other submerged settings
- Automated Options: With float switches or electrodes, Submersible Pumps can automatically adjust based on liquid levels, minimising downtime and manual intervention
- Reliability: Designed to be water-tight, Submersible Pumps are protected from external contaminants and environmental factors
- Quiet Operation: Underwater operation minimises noise, making them ideal for residential and noise-sensitive areas
- Ease of Installation: Often lighter and more compact than equivalent dry-mounted pumps. Additionally, Submersible Pumps don’t require extensive infrastructure like pump houses or above-ground systems
- Durability: They are designed to withstand high pressures and extreme conditions underwater, and are designed with materials that resist corrosion, extending their lifespan in harsh environments
- Cost-Effective: The design ensures operational longevity, while the sealed motor and fewer moving parts reduce the frequency and cost of repairs
- Safety: As the pump operates within the fluid, the risk of spills or leaks at the surface is reduced. Additionally, they offer electrical safety owing to specialised insulation that prevents short-circuiting underwater
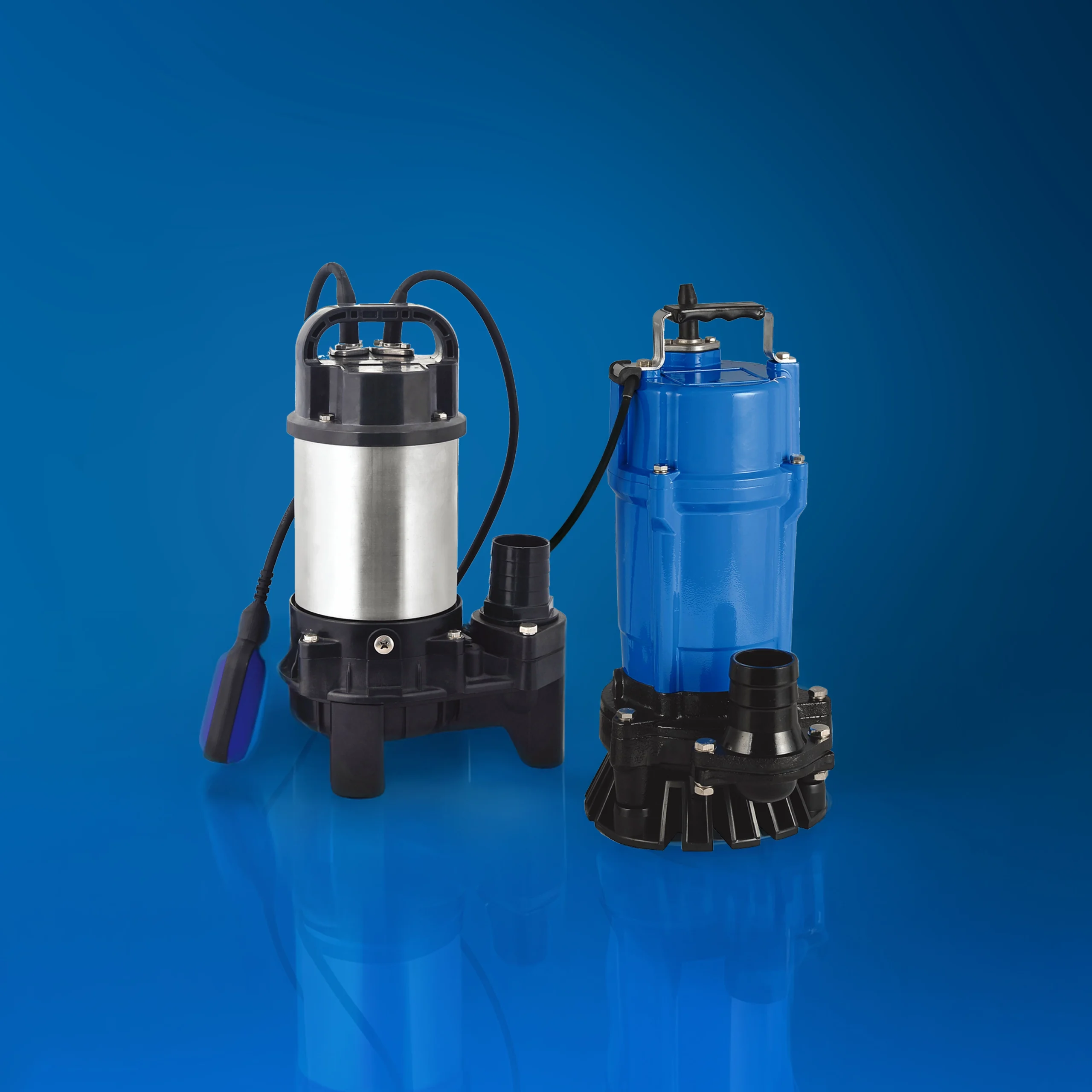
Applications for Submersible Pumps
Submersible Pumps are versatile and robust, capable of handling everything from clean water to slurry-laden fluids with high solids content. Common applications, including demand and market drivers, include:
Municipal & Residential Water Management:
- High Demand: Municipal water supply, sewage systems, and flood control dominate in many regions due to urbanisation and population growth
- Market Drivers: Infrastructure development and wastewater management regulations
Agriculture:
- Significant Demand: Irrigation and livestock watering are crucial in regions with large agricultural activities, especially in developing countries
- Market Drivers: Water scarcity and the need for efficient irrigation systems
Industrial:
- Rising Demand: Industries like Oil & Gas, Power Generation, and Mining require robust Submersible Pumps for hard environments
- Market Drivers: Increasing industrialisation and energy production needs#
Construction:
- Moderate Demand: Dewatering applications in construction and infrastructure projects remain consistent, especially in areas with high construction activity
- Market Drivers: Growth in urban construction and infrastructure
Residential:
- Steady Demand: Basement waterproofing, fountains, and small-scale water supply systems
- Market Drivers: Rising middle-class population and home improvement trends
Emergency & Disaster Relief:
- Seasonal Demand: Pumps used for flood control firefighting see spikes in demand during emergency situations
- Market Drivers: Climate change and increased frequency of extreme weather events
Marine & Offshore:
- Niche Demand: Limited to specific industries like shipping and offshore oil rigs
Market Drivers: Growth in offshore oil exploration and shipping industries
Submersible Pumps vs Water Pumps vs Sump Pumps
Understanding the differences between these pump types is essential for selecting the right solution:
Feature |
Submersible Pump | Water Pump | Sump Pump |
Design | Fully submerged in fluid | Surface or submerged types available | Submersible or pedestal |
Primary Application | Industrial fluids, slurry, dewatering | General water transfer, circulation | Drainage and overflow prevention |
Solids Handling | Yes | Varies by model | Minimal |
Automatic Operation | Yes (float switches available) | Typically manual | Yes (float switch mechanism) |
Tapflo UK Range of Submersible Pumps
Our Submersible Pumps, offering various impeller options that maintain product integrity, also feature automatic level control and protection against reverse operation, ensuring efficient and reliable operation.
- Flow:16m³/hr
- Head: 18m
- Max temperature: 40°C
- Flow: 14m³/hr
- Head: 11.5m
- Max temperature: 39°C
- Flow: 147m³/hr
- Head: 40m
- Max temperature: 40°C
Heavy Duty Sludge & Slurry Pump:
- Flow: 60³/hr
- Head: 30m
- Max temperature: 40°C
- Flow: 22.2³/hr
- Head: 13.5m
- Max temperature: 39°C
- Flow: 13.2m³/hr
- Head: 13m
- Max temperature: 40°C
Stainless Steel Dewatering Pump:
- Flow: 30m³/hr
- Head: 21m
- Max temperature: 40°C
- Flow: 1600m³/hr
- Head: 95m
- Max temperature: 40°C
What Pump Do I Need for Large-Scale Operations?
For larger-scale Dewatering, Wellpointing and Flood Control needs, our Diesel-Driven, Electric, and Tractor-Driven Pump Sets step in to handle the most demanding tasks. View our full range here, or take a look at our Guide to Dewatering to ensure you choose the correct solution for your operational needs.
Advantages of These Sets:
- Cost Efficiency & Reliability: Designed for the lowest total cost of ownership, our pumps deliver unmatched reliability with 1,500-hour service intervals on DriveOn engines, reducing maintenance and energy costs
- Compact, Mobile, & Quiet: Industry-leading compact designs ensure portability, while sound-attenuated canopies minimise noise for less disruption on-site
- Durability & Longevity: Built with wear-resistant materials and innovative features, like a pressure relief chamber to prevent water ingress, and an oil chamber to cool the mechanical seal during dry suction
- Precision & Performance: Precision-tested for suction lift accuracy within 5%, outperforming the 15% industry standard, while an oil-free priming system ensures clean and efficient operation
- Industry-Leading Support: Backed by leading Dutch partner, BBA Pumps, offering a 4-year warranty for peace of mind and long-term performance
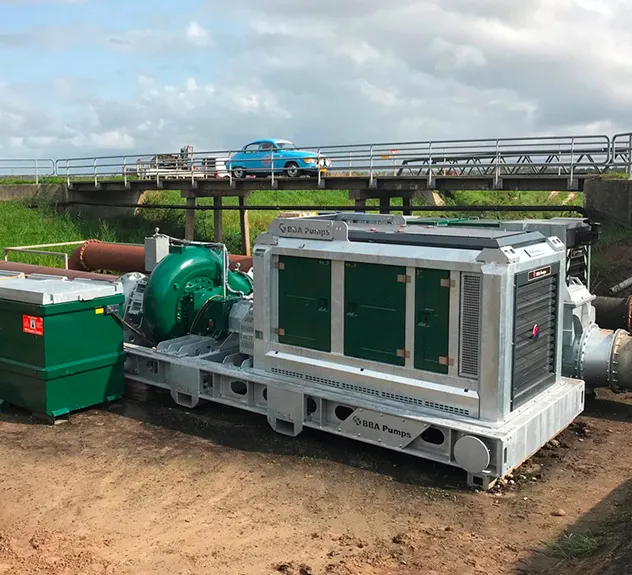
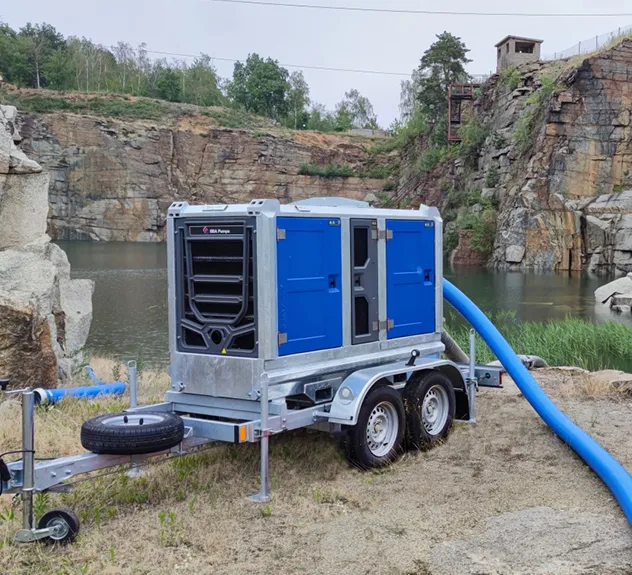
Market Insights Driving Submersible Pump Demand
- Construction Industry Boom: Investments in infrastructure, particularly in Water and Wastewater Treatment facilities, are significantly propelling the growth of the Submersible Pump market
- Global Trends: Urbanisation in certain regions is driving increased infrastructure spending, creating ripple effects in the Water Management and Power sectors
- Market Segments: Since 2021, Water and Wastewater dominated the Submersible Pump market, driven by government regulations and ease of operation, while Oil & Gas emerged as the fastest-growing sector, with the market expected to grow at an annual compound rate of 5.2% from 2023 – 2030
- Regional Dynamics: Europe remains a strong market, supported by irrigation policies and urban development. Notably, Germany leads in market share, with the UK showing the fastest growth in the region
(Source: Market Research Future, Submersible Pumps Market)
Tapflo UK offers a comprehensive range of Submersible, Vertical Immersion, and Diesel-Driven Pumps to name a few. Whether you’re managing wastewater, dewatering a mine, or ensuring site safety during floods, we have the expertise and equipment to meet your operational requirements.
For more information on Submersible Solutions and how our range can assist with your specific needs, contact us today.