In the ceramics industry, transferring and handling ceramic slurry, also known as slip, poses unique challenges for standard pumping systems. This highly abrasive, viscous material is notorious for causing wear and tear on conventional pump types, leading to frequent downtimes, maintenance issues, and rising costs. Understanding ceramic slurry’s characteristics and choosing the right pump configuration can make all the difference in efficiency, durability, and cost-effectiveness.
What is Ceramic Slurry (Slip)?
Ceramic slurry is a dense, abrasive mixture of ceramic powders, binders, and liquid, typically used in ceramics manufacturing for processes like casting, forming, and moulding. Commonly known as “slip,” it includes ceramic flour and other ingredients that create a smooth, homogeneous mixture suitable for precise moulding applications. This mixture often contains deflocculants, such as sodium silicate, which help control its consistency and reduce water content, producing a more concentrated and stronger final product. However, this drier, highly viscous slurry is challenging to pump and requires specialised pump solutions.
Applications in the Ceramic Slurry Industry
The ceramics industry uses slurry in a wide variety of products and processes, including:
- Tableware and Tiles: Slip is cast to create dishes, mugs, and decorative tiles
- Sanitaryware: Used in the manufacture of sinks, toilets, and bathtubs
- Refractory Materials and Bricks: Ceramic slurry is critical for creating materials that withstand extreme temperatures, such as those used in kilns and furnaces
- Decorative Glazes: Ceramic glazes are often slip-based, applied to surfaces before firing to enhance aesthetic appeal and durability
- Slurry Recovery and Waste Management: Handling wash water and recovering ceramic materials for reuse in production
With a range of applications for this industry, ceramic slurry handling requires pumps that can maintain efficiency and longevity across varied operational demands.
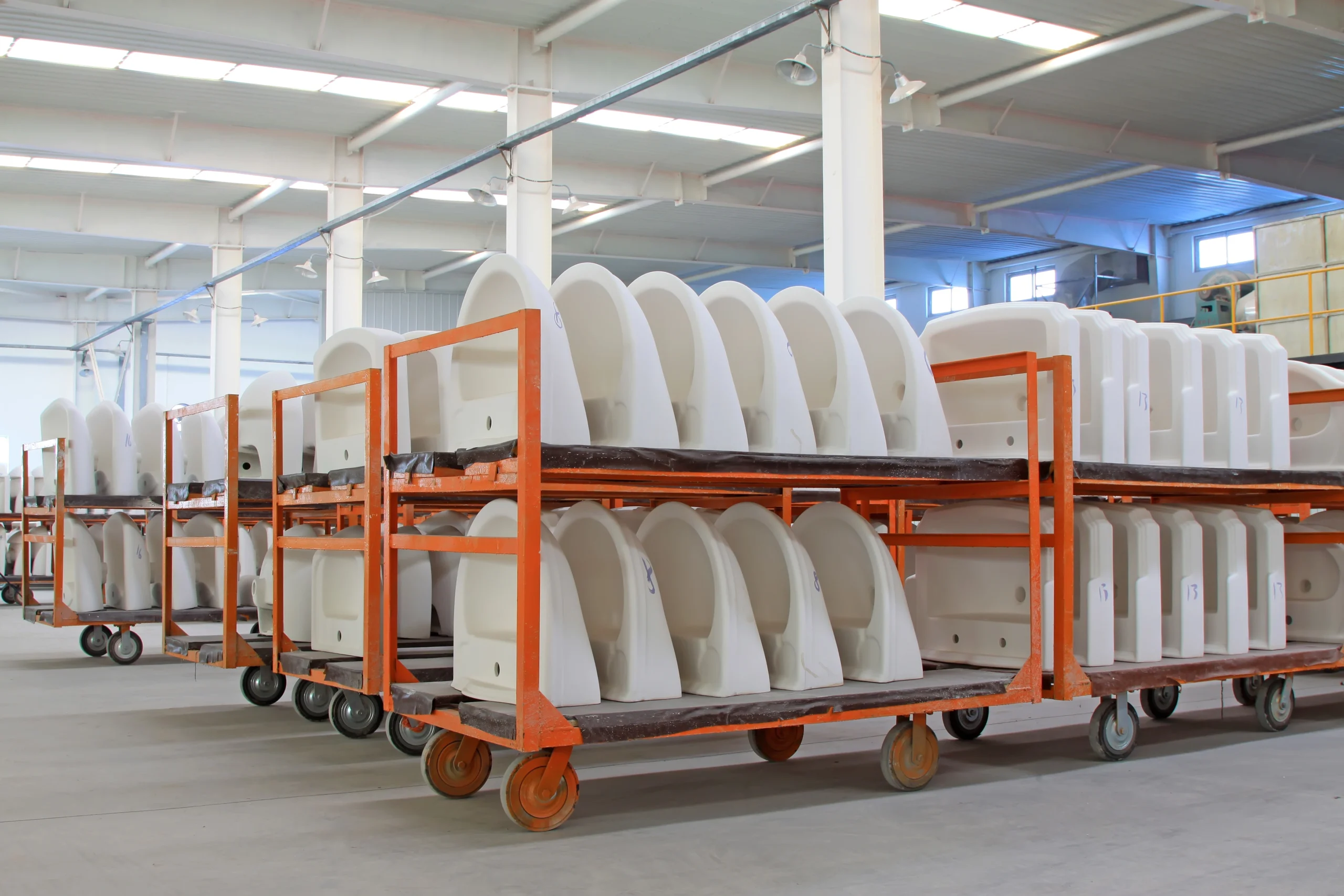
Key Pump Considerations for Ceramic Slurry
Pumping ceramic slurry is particularly demanding due to its abrasive and viscous nature. Here are the primary considerations when selecting a pump for ceramic slurry applications:
- Abrasiveness: Ceramic slurry acts like sandpaper on pump components, needing highly wear-resistant materials
- Viscosity: Slurry’s high viscosity demands a pump with sufficient power and design to handle thick, cohesive mixtures without clogging or losing flow efficiency
- Variable Composition: Slurry composition may vary depending on storage conditions, affecting flow properties and pump performance
- Maintenance Requirements: Frequent maintenance is a major concern; reducing downtime through durable, low-maintenance solutions is essential to minimise costs
Other Pump Technologies
While other pumps haves some usage within the ceramics industry, there are some potentially problematic technologies we’ve used within highly abrasive slip application, such as:
- Peristaltic Pumps: These pumps tend to experience rapid wear and tear with abrasive fluids, causing frequent hose or casing damage
- Progressive Cavity Pumps: While ideal for less abrasive applications, Progressive Cavity Pumps struggle with ceramic slurry’s abrasiveness, resulting in high maintenance costs and frequent rotor and stator replacements
- Flexible Impeller Pumps: Ideal for solids handling, however highly abrasive slip will cause damage to the impeller itself, causing further wear and tear, requiring more maintenance
- Standard Diaphragm Pumps: Although commonly used in industrial applications, standard Diaphragm Pumps often suffer from component degradation due to the slurry’s abrasive particles, leading to frequent part replacements. A special configuration of Diaphragm Pump is required for this industry, as seen in this Case Study
Key Features of Pumps Recommended for Ceramic Slurry
After extensive testing and refinement, we’ve identified the key features necessary for a reliable, long-lasting pump in ceramic slurry applications:
- Robust Materials for Abrasion Resistance: High-density polyethylene (HDPE) and polyurethane components resist wear and tear, increasing pump longevity
- Thick, Reinforced Casing: A solid, thick-walled housing prevents cracking and extends operational life
- Specialised Valves and Seals: Using abrasion-resistant materials like NBR for valve balls and diaphragms provides long-term durability, reducing the need for frequent replacement
- High Flow Rate Capacity: Pumps designed for a higher flow rate operate more efficiently in high-demand ceramic applications
- Low Maintenance Design: Pumps with minimal moving parts and advanced sealing technology reduce maintenance requirements, limiting downtime and lowering total costs
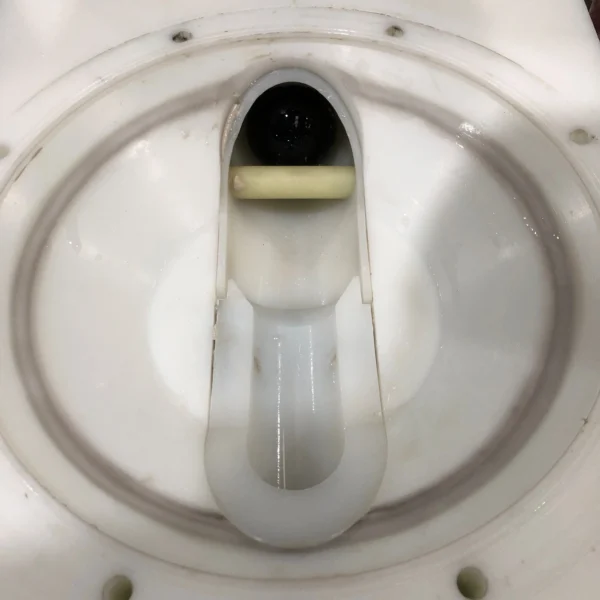
Trusted Partner in the Ceramic Industry
With over 25 years of experience working with ceramics manufacturers across the UK, we’ve developed pump solutions tailored specifically to handle ceramic slurry. Here’s why our customers trust our solutions for their challenging applications:
- Proven Durability: Our pumps operate continuously with minimal part replacements, outperforming standard pumps and reducing downtime significantly
- Cost-Effective Operation: The extended lifespan and minimal maintenance requirements of our pumps yield substantial long-term savings for our clients
- Custom Solutions: We offer a range of pump sizes, from 1” to 2”, to meet diverse production needs, including larger pumps for high-abrasion environments. This flexibility ensures that each customer gets the optimal configuration for their specific application
- Real-World Success: Our specialised pump design has been proven in ceramic applications worldwide, with over 30 units currently in operation at a leading ceramics manufacturer in the UK. Our client has reported improved production efficiency and reduced maintenance costs, affirming our commitment to quality and performance
If you’re looking for a durable, efficient solution to handle ceramic slurry, our customised pump configurations provide an answer to the challenges of wear, maintenance, and downtime. Trusted by leading ceramic manufacturers, we offer pumps built to thrive in high-abrasion, high-viscosity environments.
Contact us today to learn more about how our pumps can enhance your production process, reduce costs, and deliver reliability where it matters most.