What is a Peristaltic Pump?
A Peristaltic Pump, also commonly known as a ‘Tubing Pump’ or ‘Roller Pump’, is a type of Rotary Positive Displacement Pump and is one of the most versatile and flexible pump systems available on the market today. A unique design feature of Peristaltic Pumps is that the hose is the only part within the pump that comes into contact with the fluid. This ensures that the pump is sealless and is one of the main reasons they are so reliable.
The type of hose used within the pump is chosen based on the application to ensure the material suits the process fluid.
How Does a Peristaltic Pump Work?
As seen in the image below, a Peristaltic Pump works by either two shoes (high-pressure applications) or rollers (low-pressure applications) rotating on a wheel inside of the pump and compressing an internal hose, which then forces through a certain quantity of fluid. The hose inside of a Peristaltic Pump is designed to return to its original shape after the shoes or rollers have passed over, so the quantity and flow of fluid are consistently maintained.
This pump operation is also where Peristaltic Pumps get their name from. The term “peristalsis” originates from the biological sense where muscles contract in our stomach to allow food to push through. A similar process happens when a Peristaltic Pump is in operation to allow for a variety of applications to enter the pump and effectively be passed through to the suction side of the pump, allowing more fluid to continue to enter from the pump casing.
Working Principle of a Peristaltic Pump:
Why Use a Peristaltic Pump for Fluid Transfer?
Peristaltic Pumps are an excellent option for fluids that need to be kept clean and sterile, such as food and beverage applications, due to no contamination occurring in the pump. As mentioned before, the interior hose is the only part of the pump to come in contact with the application, which completely minimises the risk of bacteria growth, making the pump ideal for the hygienic industry.
Peristaltic Pumps come with a number of benefits, some of which are:
-
- Fully self-priming up to 9.8 meters – not many other pumps on the market can produce that kind of suction!
- Damage-free when dry running
- Outlet pressures of up to 15 Bar
- Suitable for corrosive, aggressive, and viscous fluids
- Suitable for fluids containing particles
- Very easy maintenance
- Safety – the only part of the pump that comes into contact with the fluid is the hose!
- Reversible flow
- Heavy-duty bearings, greased for life
- ATEX available for hazardous environments and applications
What is CIP Peristaltic Pump?
CIP stands for “Clean in Place” and is an effective cleaning solution often used within the food, cosmetics, and pharmaceutical markets. CIP Pumps allow cleaning in place of the pumping equipment including tanks and pipes, without the need to dismantle. This includes sterilisation which can be carried out at temperatures up to 85ºC.
If you need a Peristaltic Pump but can’t risk any kind of contamination from the application you’re pumping, a CIP Hose Pump would be an ideal option.
For more information, read our article on CIP Pumps.
Information Required to Quote a Peristaltic Pump
Below is a list of details you’ll need to know in order to select the correct Peristaltic Pump for your requirements.
- Fluid description
- Viscosity (shear thinning or thickening)
- % of solids and particle size
- Temperature
- PH level
- The flow rate or range
- Suction and discharge pressures
- Precise Duty cycle (continuous or intermittent) real pump running time
- Power Supply available
Hose Materials
Hoses can be supplied in the below materials to suit a wide variety of applications:
The price of the hose usually works out to around 8 – 10% of the cost of the pump.
Applications and Industries
Peristaltic Pumps are suited for both low & high-pressure transfer, metering and dosing of low or high viscous applications, pasty, pure, neutral, aggressive or abrasive liquids, those containing gases or which tend to froth, or those containing solids. The pumps are commonly used in the following industries:
- Food & Beverage: tomato sauce, mashed potatoes, gelatine, beer yeast, fish paste, olive oil, wine, egg white & yolk, edible fat, semolina, natural flavouring, cream, milk & yoghurts.
- Bakeries: water & salt mixtures, natural flavourings, fats, fruit cake dough/mixture (i.e. fruit cake has nuts and fruit pieces that need to stay whole).
- Paint: water-based paint, acrylics, pigments, ink, and wall coating.
- Meat and Fish processing
- Pharmaceutical & Cosmetics: chemical dosing, liquid protein, vaccines, serum, plasma, syrups, and shampoos.
- Waste Water & Water Treatment: lime cream, ferric chloride, sodium bisulphate, fluoride, polymers, aqueous ammonia, potassium permanganate, caustic soda, activated carbon, reagent feed, coagulant, flocculants, dispersion, alum, sludge and foams.
- Chemical and Petrochemical: various acids, PVDF latex, alcohol, soap, and non-aromatic solvents.
- Pulp and Paper: latex, kaolin, paper waste sludge, various chemical dosing.
- Ceramics: barbotine, mould filling, filter press feeding. Building fibrous mortar, plaster, light concrete, and cement flooring.
- Surface Treatment: Abrasive waste fluids, acids, alkalis, paints, Electrolytic zinc plating, Copper, Nickel, Tin, Silver and Gold plating, Alcalic zinc, Zinc-iron, Zinc-nickel, Hexavalent Chromium-free plating, Chromates / Passivation, Acid zinc
- Anaerobic Digestion: Processed Food & General Waste, Feedstock, Digestate, Waste Sludge
- Mineral Processing: sludge with a viscosity of up to 60,000 cPs, clay up to 800g/l, particle size: 30 mm, lead sulphate, pyrite, cyanide, various acids.
- Agricultural: manure, fertilizer sugar mills, molasses, liquid sugar and various chemicals.
Why Choose a Peristaltic Pump over a Diaphragm Pump?
So now all the important information on Peristaltic Pumps has been covered, what sets it apart from one of the most used pumps on the market?
- Air Operated Diaphragm Pumps require a compressed air supply to drive them. If this does not already exist it can be very expensive to install. Even the best-maintained air supply systems are inefficient with at least 30% air leakage. The energy costs of supplying air for a Diaphragm Pump are much higher than for a Peristaltic Pump.
- Air pressure limits the discharge pressure – it just stops pumping beyond its limits.
- Changing pumped fluid is complex as cleaning a Diaphragm Pump is difficult, often requiring a complete strip-down. Peristaltic Pumps offer a quick maintenance schedule for their pumping elements. Simply change the tube and you’ve created a new pump!
- The difficulty in accurately controlling the air supply makes a Diaphragm Pump a poor choice for metering duties.
- Even Double Diaphragm Pumps have a high level of pulsation.
- As with all Diaphragm Pumps, AODDs generally rely on ball valves. These do not work well unless there is positive back pressure to close them between cycles. They are prone to abrasive wear and can clog with crystals, fibres or solidifying fluids such as inks and powders.
- Whilst the initial purchase cost is lower, the cost of ownership can be much higher due to energy and maintenance costs.
Previous Projects
Tapflo UK has worked on a number of large-scale projects involving Peristaltic Pumps, some of which are featured below.
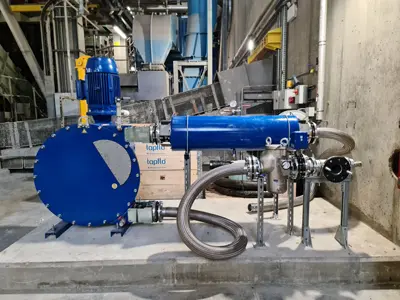
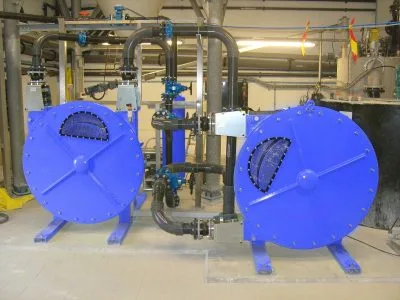
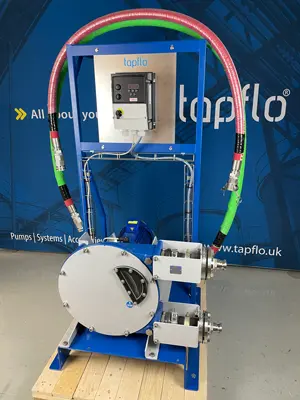
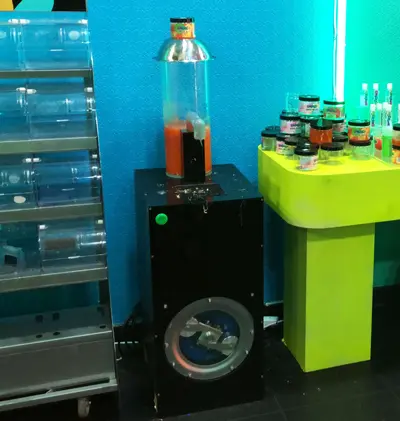
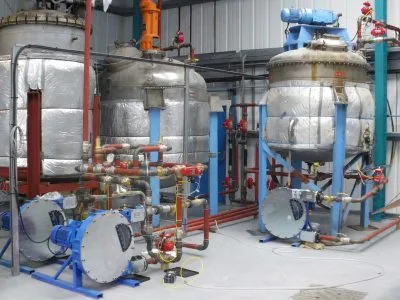