Our client has been at the forefront of cutting-edge engineering design, fabrication and installation for over 30 years. With a reputation to uphold on a project with national interest and media scrutiny, they needed a turnkey pump solution they could depend upon.
Application Details
The customer needed to circulate and pump Sodium Silicate Solution, a liquid that can be abrasive to pumps over time, into shuttle tanks. The tanks then transport the solution to be mixed to form an active filling grout for injection in the annular void produced during boring.
Pump Solution
In order for our team of Technical Engineers to provide an effective and efficient pump solution, we first had to fully understand the requirements of the project and the estimated demands put on the pump. We achieved a full brief by working closely with our client’s team of engineers over site visits and multiple conference calls and were able to assist with a bespoke skid design.
We supplied 2 pumps for transfer working at 60m3/hr at 2 Bar discharge, as well as 1 pump for re-circulation working at 35m3/hr at 42 Bar discharge, both being used for 30-minute intervals.
The Salvatore Robuschi RC pumps chosen for this project are Close Coupled End Suction Pumps fitted with Recess Vortex Impellers, allowing for the transfer of large solids (<70% ø of the inlet size). The impellers design, along with the centrifugal motion imposed on the fluid, allows the majority of the solids to be kept away from the impeller and mechanical seal. This ensures that wearing of these parts from the abrasive Sodium Silicate Solution is kept to a minimum. In return, this helps increase the lifespan of the pump and lowers maintenance costs while keeping downtime to a minimum.
Pumps were fitted with SiC/SiC mechanical seals to ensure long working life.
The 2x transfer pumps were also fitted with 4Pole motors to ensure a long working lifetime by operating at a lower speed whilst still achieving duty.
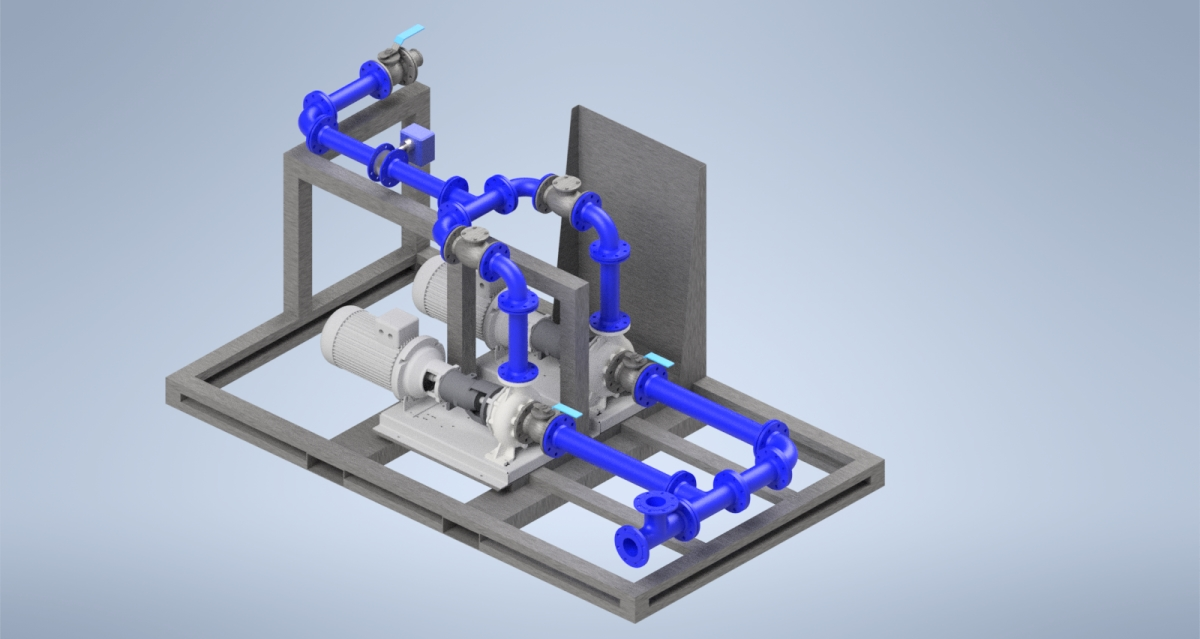
Features & Benefits
- Free Passage of Large Solids
- Resistance to Wear
- One Casing Cover fits 14 Different Sealing Systems
- ISO 5199 – EN 25199 Heavy Duty Bearings
- Modular Execution
- 14 Different Sealing Systems, 1 Chamber
If you’re looking for a complete solution, our team of Technical Engineers are available to design and build a unit that meets all your requirements.