We were contacted by a UK start-up company that had developed a great idea to use green waste to create sustainable faux leather. After outlining their functional, application & system requirements, we were able to design & provide the customer with a complete turnkey skid system that included a self-priming flexible impeller pump, hygienic trolley w/ drip tray, variable speed drive, flow meter w/ totaliser & sight glass along with custom pipework & valving layout.
The mobile solution fitted their requirements perfectly as it would give them the versatility and mobility that they required in their facility.
Equipment Supplied
Pump Type | Self-Priming, Bi-Directional, Flexible Impeller Pump |
Fluid | Faux Leather |
Rated Capacity | 80 l/min @ 10 m Head |
Max Temperature | 90°C |
Required Suction Lift | 2 m |
Capable Suction Lift | 6m |
Max Solids Passage | 10mm |
Inlet / Outlet Ports | 1.5″ Tri-Clamp DIN 32676, Including Counter Parts |
Vent Ports | Automatic air vent on discharge |
Motor | 1.5 kW / 2 Pole / 50 Hz |
Body & Impeller Material | Stainless Steel 316 w/ Silicon VMQ Impeller |
Seal Type | Single Mechanical Seal SiC / SiC / EPDM |
Fitted Accessories | Temperature switch set to 90oC
Forced ventilation |
Control details | IP66 4kW switched Inverter, Flowmeter & Totaliser w/ mains isolation switch |
Solution & Support Offered
We provided our customer with the solution shown on the right. This incorporates a trolley with an integrated drip tray, flow meter, flow totaliser, sample point, sight glass, suction strainer & flexible impeller pump with forced ventilation.
Overall Dimensions: 1250 x 760 x 950 mm (L x W x H)
The customer has some mixing vessels that required a pump system to not only circulate the media to ensure even mixing but also to be used as a dispensing system for their moulds. The system needed to be self-priming as well as capable of withstanding 90oC and allow the client to measure the flow rate and to reduce it if required via the use of the trolley mounted inverter drive system.
Due to the temperatures involved, the speed range required and for the longevity of the system, the pump was equipped with forced ventilation, a VMQ Silicon impeller as well as a dry-run temperature switch which is wired to the inverter’s emergency stop/trip system to stop the pump when tripped. As well as forced ventilation the pump is equipped with a SiC / SiC / EPDM single mechanical seal to combat the solids in suspension and the temperature range of the fluid. The pump was also equipped with an automatic bypass which will allow the pump to run even if all connections are blanked by allowing the fluid to continually flow around the pump head.
To allow our customers to take samples of the material that is being pumped we included a hygienic sample point. All the pipework and where possible the main components are hygienic to allow for minimal contamination between batches of the media, allowing our customer to have a more reliable end product.
Full in-house testing and calibration were conducted before shipment to ensure functionality before shipment and our technical team went to the site once installed to ensure that the pump was installed correctly and to fix any minor issues that arrived from testing in situ.
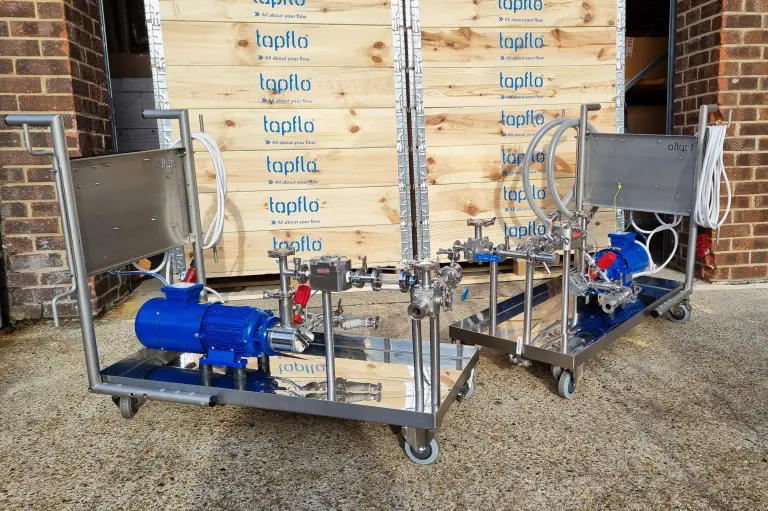