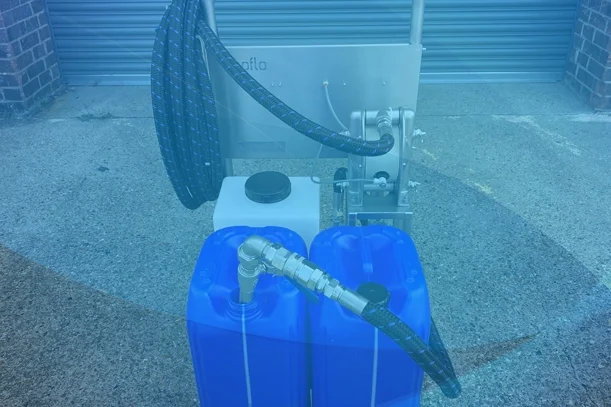
We were approached by one of our trusted distributors for the supply of a bespoke version of our popular TPUK-MDU-20 Mobile Decanting Systems for use in a Cider Brewery. Thanks to our knowledge and experience in designing and producing Bespoke Mobile Decanting Systems, we were perfectly placed to come up with an ideal solution matching the end user’s requirements. Our in-house design team liaised with the client to ensure that the system was suitable for their needs, ensuring we incorporated all the features and functionality they required for the process going forward.
Application Details
Recently, one of our trusted distributors were in the market for a bespoke version of our popular TPUK-MDU-20 Mobile Decanting Systems for use in a Cider Brewery. Our customer wanted the system to dose 5 to 10 Litres of Hydrogen Peroxide @ 35% concentration from an on-board reservoir into several storage vessels within their tank farm as part of a CIP procedure.
The customer also wanted to have the facility to swap over to a secondary on-board Water Reservoir to facilitate a 2 to 10 Litre water flush of the tanks and associated pipework/hosing. By doing this, there would be no chemicals left in the lines which would put the operator at any risk when detaching the lines from the storage vessels once the transfers have been completed.
To further reduce risk and cross contamination, the customer also wanted each on-board reservoir to be double isolated via isolation valves and have a 3-way valve at the pump suction to facilitate easy and quick changeover between the reservoirs. The requested 10m discharge hose assembly was also requested to be fitted with a non-drip point of dispense valve (POD Valve).
System Specification
Following these discussions, we were able to present our preliminary designs to the customer for their review and approval. The system developed and supplied comprised of the following:
- TL70 STT – ¾” Air Operated Diaphragm Pump in AISI 316L with PTFE Diaphragms & Valve Balls fitted with Manual Ball Lifters. The Manual Ball Lifters fitted onto all 4 of the pump’s ball valves can be manually lifted to drain the fluid in the pump and discharge line back into either the water tank or jerry can.
- Air Treatment & Control Set – Manual On/Off Valve, Filter Regulator, Needle Valve, Modified Muffler, Blocking Needle Valve & Interconnecting Hosing – all located next to the batcher on the back of the trolley for ease of setting and use. This facilitates isolation of the incoming mains air supply and flow and pressure regulation of the pump, as well as suitable set-up for batch controlling.
- TPUK-BP – Pneumatic Batch Controller – Mounted to operator side of Trolley Brace Bar for ease of use. This provides the operator with the facility to batch the required 2, 5 & 10 Litre batches of Hydrogen Peroxide and Water onto the process. The pump can also be manually primed with the controller before starting the batch.
- 20 Litre PE Water Storage Tank with ½” Bottom Outlet & 4″‘ Vented Screw Cap Lid – it can be filled via the Lid and emptied via the bottom outlet. Fitted with a 2-Piece Manual Isolation Ball Valve in AISI 316/PTFE.
- Modified Tapflo HM0S Hygienic Trolley with Drip Pan (AISI 304 – Glass Blasted), Drainage Valve, 2 x Removable Handles & Brace Bar, Discharge Hose Stowage, Pump Stand, Container Stay Points (can fit 2 x 20-25 Litre Jerry Cans at the front) & 4 x Castors (Rear Swivel with Brake).
- Pump Suction Side Accessories & Fittings: The Pump Suction Assembly was positioned downwards and underneath the Pump Stand with a 3-Way T-Port Ball Valve for Fluid Source Control with 0.5 m Convoluted PTFE Hosing (PP Overbraid) onto the outlet of the 20 Litre Water Storage Tank & 1.0 m Convoluted PTFE Hosing (PP Overbraid) onto the Suction Lance for Hydrogen Peroxide Jerry Can (~500 mm w/ Chamfer Cut). The Suction Lance & Hosing were also fitted with AISI 316/Viton Parker SnapTite H Valved Quick Release Adaptors for easy, non-spill connection and disconnection from interconnecting components.
- Pump Discharge Side Accessories & Fittings: The Pump Discharge was fitted with a 2-Piece Manual Isolation Ball Valve in AISI 316/PTFE and 10 m of Convoluted PTFE Hosing (PP Overbraid) & POD Valve. An AISI 316/Viton Parker SnapTite H Valved Quick Release Adaptor was used in between the isolation ball valve and hose assembly to facilitate easy, non-spill connection and disconnection.
This system is a compact workhorse with a footprint of 925mm x 687mm x 968mm (L x W x H) to enable easy transportation in and around doorways and tight spaces in the tank farm.
Render to Reality
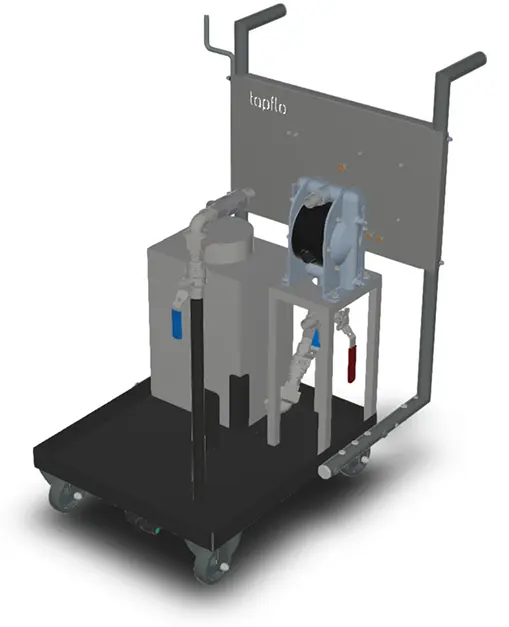
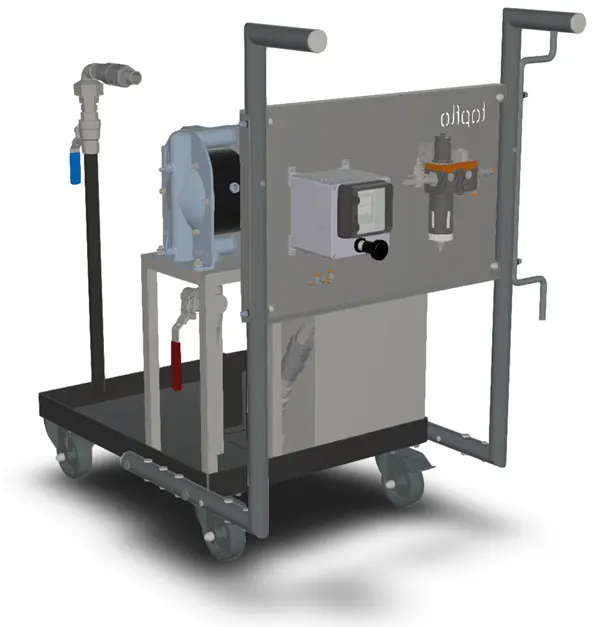
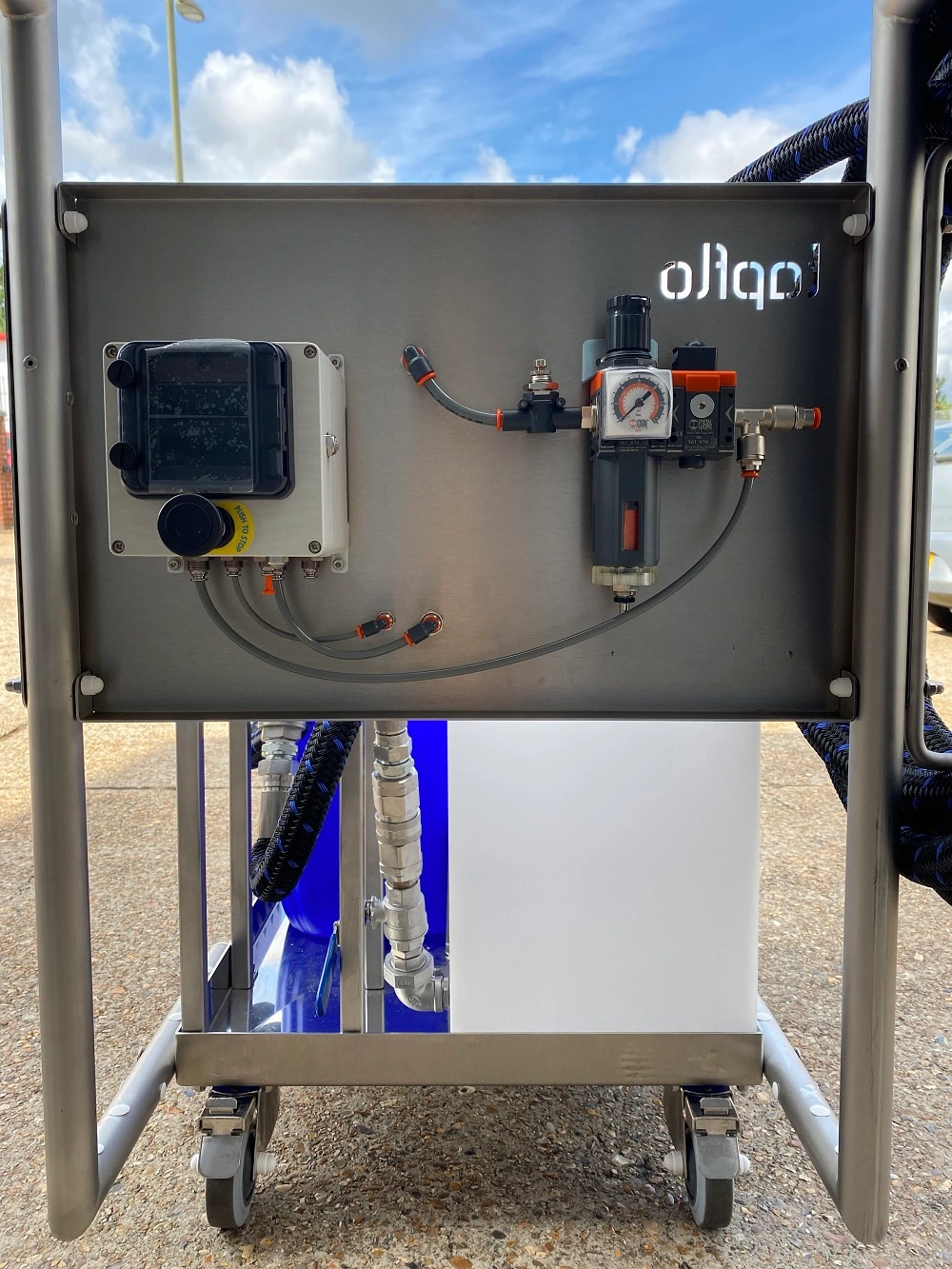
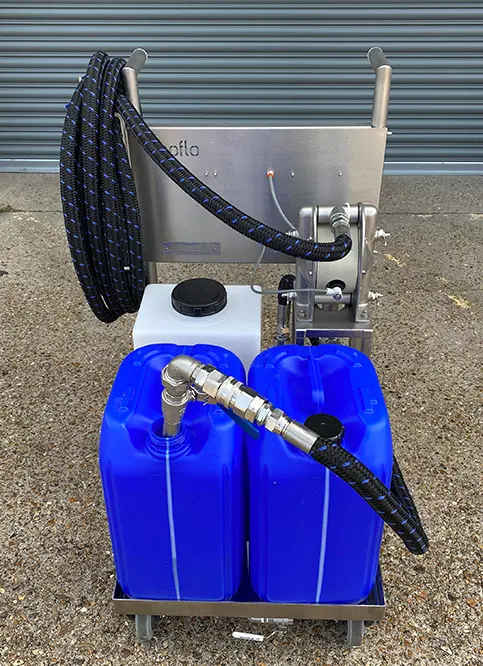
Explainer Video
Our Technical Manager, Edward Shaw, explains the application and system further in the video below: